We use real wood for all our products. Sourced from top lumber mills across the U.S., our selection features Red Grandis and Southern Pine.
Natural variations—such as knot structure, grain color, and patterns—are part of what makes real wood so beautiful. These unique features are why real wood is chosen to enhance any home.
GRADING OF LUMBER
Although each type of wood has its own grading system, the purpose is the same: to establish what is and isn’t acceptable between buyer and seller.
Boards are first graded at the lumber mill using standardized grading. During our production process, we re-inspect, re-grade, and hand-select each board. Even with this extra grading, wood is a natural product and therefore, each piece is going to be uniquely different. Synergy’s additional grading process results in an easy-to-install product that is 99% usable, reducing on-site installation waste from 30% to 5% or less.
Every board that is delivered to a job site is usable. A guide to Synergy Grading is available. Visit the page “How To Use What’s Delivered”.
WHAT SYNERGY ALLOWS
Synergy grades each piece of lumber following industry standards, but we also assess factors like side bend and checks.
Checks: These are separations in the wood, typically occurring across or through the annual growth rings as a result of seasoning.
Side Bend: This occurs when a board has a slight axial curve when laid flat. A diagram of this is shown on our website “How To Use What’s Delivered”.
Synergy allows the following side bend during our manufacturing process (based on length to curve):
- 4’ to 7’ boards; up to 1/4” side bend
- 7.1/2’ to 8’ boards; up to 3/8” side bend
- 9.1/2’ to 10’ boards; up to 1/2” side bend
- 11.1/2’ boards; up to 5/8” side bend
- 12’ to 14’ boards; up to 3/4” side bend
THE SYNERGY PROCESS
Tongue and Groove
The first step in producing our tongue-and-groove products is running the raw wood through a molder, which adds the T&G profile to the long edge of each board.
T&G with End Matching
The wood is then hand-sorted and inspected for any objectionable defects such as holes, splits, cracks, and loose or missing knots. The visible defects are removed and then each piece is end-matched with a male/female interlocking end.
Sanding. Sanding. Sanding.
After the end matching process, the board is sanded in multiple steps – making them ready for the staining process.
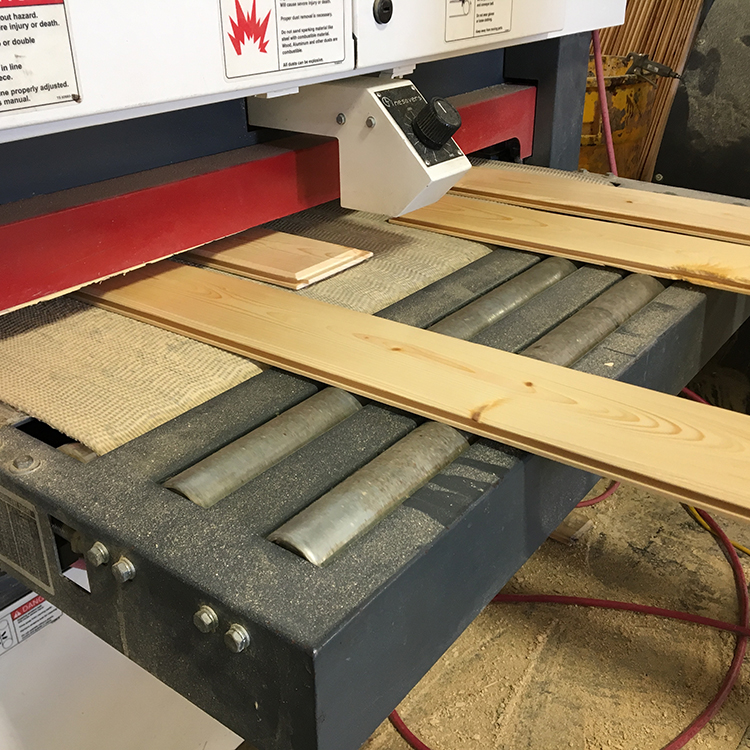
Horizontal lines are caused by the molder’s knives as the boards are cut. Without multiple sanding passes, these marks will remain visible, especially once stain is applied. If you’ve used raw T&G from a lumber yard and stained it on-site, you’ve likely encountered this issue firsthand.
Hand Wiped Stain
Unlike other companies or on-site installers, we hand-wipe each piece after applying stain, “pushing” the stain deeper into the wood. This results in a richer, more consistent color that can’t be achieved on-site.
Sign Sealed Delivered…
After our hand-stained boards complete a thorough drying process, we apply a clear sealer coat of exterior-grade polyurethane. This sealer envelops the porous wood, preventing the next coat from being overly absorbed. After a second drying cycle, the boards are lightly sanded and prepared for the final coat of exterior-grade polyurethane.
Customers choose Synergy for our handcrafted wood boards that are naturally beautiful, exceptionally durable, and easy-to-install. We handle the time-consuming steps, delivering a “ready-to-install” product that reduces both labor and waste.
SYNERGY SAMPLES
To truly appreciate the color and texture of real wood, we recommend ordering Synergy Wood samples. Click here for free solid wood color samples!
If you’ve received a sample of our Southern Pine, please note that all samples are cut from #2 mill-graded lumber. While many samples may not show knots, this is NOT typical of our #2 or Standard graded products, which will have knots. Please keep this in mind when making your purchase.
COLOR VARIATION
Wood is a natural product, so variations in color and grain pattern are to be expected when stained.
In some woods, including Southern Pine, heartwood is naturally present and visible through all colors. Over time, exposure to light can cause the heartwood to age or darken, potentially producing yellowish or reddish streaks.
Pine also contains knots and resin (sap). Boards with higher resin content will be heavier and may absorb stain differently, often resulting in a lighter appearance.
5 YEAR WARRANTY
Synergy Wood products are designed for interior walls, ceilings, and covered exterior ceilings. We do not recommend or warranty products exposed to direct sunlight or moisture. For more details, click here to view our 5-year limited warranty.
In the unlikely event of a warranty claim, the end-user must provide the Job Number and Manufacture Date, which can be found on the packaging delivered to the job site. Claims cannot be processed without this information.
We’ve found that boards with a side bend can be easily straightened with light pressure when placed on edge. If a board with a side bend is discovered during installation and is undesirable, it can still be used. Refer to our guide, ‘How to Use What’s Delivered,’ for more information.
HELPFUL DEFINITIONS
Chipped grain means that a part of the surface is chipped or broken out in very short particles below the line of cut. It should not be classed as torn grain and, as usually found, shall not be considered a defect unless it is present more than 25% of the area.
Loosened grain means that a small portion of the wood has become loosened but not displaced.
Torn grain means that a part of the wood is torn out in dressing, and in-depth is four distinct characters; slight, medium, heavy and deep.
The medium torn grain is over 1/32”, but not more than 1/16” in depth.
Skip is an area on a piece that failed to surface. A heavy skip is one that the planer knife did not touch.
Machine burn is a darkening or charring of the wood due to overheating by the machine knives.
Machine gouge is a grooving across a piece due to the machine cutting below the desired line of cut.
A sound knot is solid across its face, as hard as the surrounding wood, and shows no indication of decay.
A medium knot is one over 3/4”, but not more than 1.1/2” in diameter.
A pith knot is a sound knot with a soft center not more than 1/4” in diameter.
Peck is decay which appears in the form of a hole, pocket, or area of soft rot usually surrounded by sound wood. Slight peck is not through the piece occupying less than 10% of the surface area.
Decay is a disintegration of the wood substance due to the action of wood-destroying fungi and is also known as dote or rot.
Machine bite is a depressed cut of the machine knives at the end of the piece.
A shake is a lengthwise separation of the wood, which occurs usually between and parallel to the rings of annual growth.
A check is a lengthwise separation of the wood, which occurs usually across the rings of annual growth.
Wane is bark, or the lack of wood or bark, from any cause on the edge or corner of a piece.
Pith is the small soft core in the structural center of the log.
Pitch is an accumulation of resinous material.